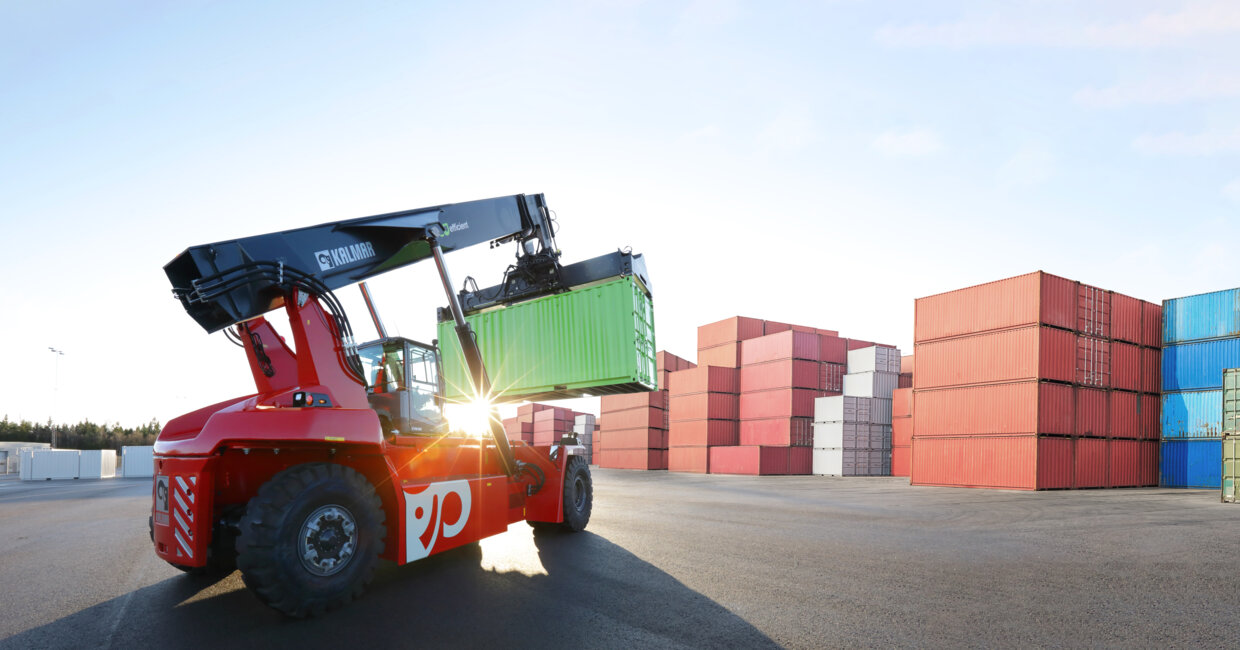
Towards eco-efficient cargo handling operations, part 4: Building the business case
Kalmar has defined a step-by-step approach to eco-efficient cargo handling operations, supporting terminal operators all the way from their early vision and targets to the implementation and ongoing optimisation of their solutions. In this part, we talk about how to evaluate future operational scenarios and validate new terminal designs, while gaining the best possible foresight into the impact of various eco-efficient solutions.
Electric equipment is rapidly gaining ground as the basis for future terminal designs across the world, as operators seek to meet stakeholder demands and ensure regulatory compliance. Electrification requires a carefully planned infrastructure strategy in addition to choosing the best type of eco-efficient equipment for each usage scenario.
Once these steps have been completed, the next task is to evaluate the future operational scenarios of the terminal and to build a strong business case for eco-efficient operations. For existing terminals, this is a multi-year journey that needs to be based on the planned future evolution of the terminal as well as global and regional trends that can be expected to impact operations.
Seeing the global picture
Based on the strategic vision, terminal operators can begin to assess the business case for eco-efficient operations. "It's crucial to understand the macro indicators that are relevant for your business," says Lasse Eriksson, Vice President, Technology, Kalmar. "You have to keep an eye on how the entire industry will change, but then you also need to be more specific about your own place in the value chain, and how it will develop. Various indicators and industry developments provide the input for the scenarios of future terminal operations, and these scenarios form the basis of the investment planning.”
An example of such an industry metric is the world Gross Domestic Product and transport demand growth index. Projecting to 2030, this index estimates that worldwide maritime container traffic will continue to increase by more than 6% per annum. Simultaneously, airfreight is projected to increase by 5.9% p.a. over the same period, with rail passenger and freight traffic worldwide growing at 2-3% p.a.
"One needs to assess how these changes will affect the operations at the terminal, as well as what other drivers there are for future growth," says Eriksson. "The projected growth in operations must then be mapped into key operational parameters, such as the number of container moves, the weight of loads moved and distances driven, and ultimately which kind of machine fleet will be needed to operate the future scenario."
"Electric equipment will often beat traditional diesel-powered solutions when considering both the capital expenditure and operating costs together, over a period of a few years."
Lower lifetime costs
Once the future operational scenario is defined and the fleet to operate that scenario starts to take shape, it is possible to analyze the total cost of ownership for each type of equipment. "TCO is obviously a key criterion for the investment, and eco-efficient solutions must also meet the business objectives of the terminal," Eriksson points out. "However, the good news is that electric equipment will often beat traditional diesel-powered solutions when considering both the capital expenditure and operating costs together, over a period of a few years."
Typically, electric equipment will require a larger up-front investment that also encompasses the required charging infrastructure. However, this expenditure can be offset by lower maintenance and energy costs over the long term. Electric equipment has fewer moving parts and longer maintenance cycles, typically costing up to 50% less to service and maintain over the lifetime of the equipment. Moreover, energy costs for electric equipment are more predictable since electricity prices have historically been more stable than those of diesel fuel.
Local differences are key
In addition to the specifics of the operational plan and equipment type, the return on investment for an eco-efficient cargo handling solution also depends on the country and region of operations.
"Projections on the future costs of fuels and energy may vary significantly from region to region, which will have a dramatic impact on the business case," notes Christopher Saavedra, Terminal Design Manager at Kalmar Automation Solutions. "Our recommendation is to always verify the calculation with sensitivity analysis, which means using different scenarios for fuel and energy costs, to see how sensitive the business case is to small variations in the basic assumptions."
Saavedra points out that the regulatory framework also varies widely across the globe, with different regions facing different opportunities and challenges on the way towards eco-efficiency. "At the moment, sustainability is a top priority especially in Europe and North America, with the latter region also focusing particularly strongly on automation. The state of the civil infrastructure and especially the power grid will have a major impact on how quickly terminals can adopt all-electric solutions. Local differences in taxation and investment incentives will also make a big difference."
Saavedra notes that it's crucial for operators to find the right balance for their level of investment, while also taking into account the existing fleets at the terminal. "You don't necessarily need to have every piece of equipment updated to the state of the art. It's also about operational flexibility. Can your terminal handle 24/7 operations or do you need additional automation to be able to scale your operations both up and down? Also, if you just upgraded everything last year, it's a different situation than if you are due for an update anyway."
"Our recommendation is to always verify the calculation with sensitivity analysis, which means using different scenarios for fuel and energy costs, to see how sensitive the business case is to small variations in the basic assumptions."
Design, simulate, verify
Once the operational scenario is defined with specific goals, and the metrics for factors such as load cycles, terminal throughput and energy consumption are known, Kalmar recommends validating the terminal design with a simulation tool. The calculations show which set of equipment will deliver the expected throughput and which kinds of savings can be achieved in the specific operations of the terminal.
"The simulation tool also considers the impact on the infrastructure, and helps define the needed charging power in order to run such operations," notes Christopher Saavedra. "The tool considers the dynamics of the operation along with charging times, in order to optimize the charging infrastructure. This means knowing exactly how many chargers and how much power is actually needed in the operations."
The key metrics to be evaluated in these simulations are the eco-efficiency parameters (such as CO2 emissions reduced), as well as monetary savings from energy and operational costs. With this approach, it is possible to validate that the business case meets the required targets, both financially and from the eco-efficiency point of view.
"At Kalmar, we have previously developed fuel and energy saving guarantees, which are based on understanding the operational scenarios in terms of distances travelled, moves per hour, the load per move, and knowing exactly how much energy our machines consume in those operations," says Lasse Eriksson. "The total cost of ownership calculation should be based on such knowledge as well, so that the operational scenario is correctly reflected in the calculations."
The fuel and energy saving guarantees can be used when deploying the new eco-efficient solutions in order to ensure that the investment will pay back as expected. "Fuel and energy savings guarantees basically mean guaranteed operating costs for the customer," says Eriksson. "From the work that we have done in deploying eco-efficient solutions at terminals around the world, we have gained great experience that will help our customers meet their eco-efficiency targets while simultaneously growing their business in a predictable way."
Related articles
Subscribe and receive updates in your email
Subscribe